As data is gathered to review how capable and stable a given process is, the presentation of the data is seen as an important factor to ensure data is communicated and understood correctly. One rigorous system which has the main principal focus of reducing variability for economic advantage is Statistical Process Control (SPC). In the past, responsibility for product quality tended to rest with the inspection department, who had very little influence in continuous improvement activities. Acting as mere "policemen", quality inspectors would provide data, and the crisis managers would follow with the "fire fighting". Even though improvements have been made regarding the investment into more technical and automated measurement systems, and placing improved problem solving procedures, it became harder for manufacturers to visualise the thought of not producing non compliant material at all.
If we look at the Figure 4, it shows a typical inspection based process outline, consisting of inputs, process, rework if necessary and the overall output. Research in this subject is well documented and discuss around the problems highlighted below:
- Employing additional resources and staff to sort the good from the bad products can become a very expensive approach, whilst adding no value to the product. Even if defects are found, the product would have been manufactured, and would only incur additional rework or scrap costs.
- There is no such thing as a faultless system. If the inspection process is incapable of assessing the good from the bad, it could resort to defective material being shipped to the customer.
- Using PASS and FAIL criteria is not informative enough to continually improve both the product and the inspection process. Variable data is generally a better choice to use oppose to attribute data.
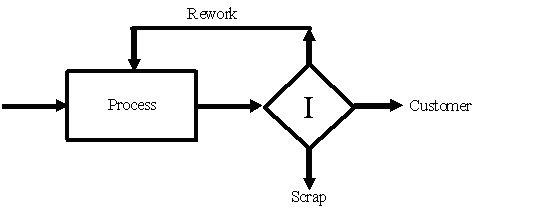
Figure 4: A generic inspection based process outline
Rather than reactive control, the SPC philosophy creates the approach of applying predictive control. This can help provide businesses with confidence into how capable their processes are and which processes require improvement or scheduled monitoring. Better still, by having the ability to prioritise necessary improvements, responsibility can be placed to people who can make a difference.
Page 8 out of 15